Conventional Pallet Rack
Conventional Pallet Rack is a cost effective storage system providing direct access to all pallets. It provides high capacity storage, is easily installed and adjusted, and has low equipment and capital costs.
Features:
- Pallets can be located, accessed and moved individually.
- Rapid handling of almost all types of palletized goods.
- Infinitely adjustable and offering a wide range of options and components to accommodate specialized needs.
- Maximizes space use in any warehouse configuration while retaining optimum product accessibility.
- Strength and rigidity prevents compression damage to goods.
- Bottom level of pallets can be stored on the floor, lowering structure costs.
Related Products
For different warehouse layouts, we also provide similar products, including Drive-In Pallet Rack, Double Deep Pallet Rack, and Very Narrow Aisle (VNA) Rack. For US market, we supply US style Teardrop Pallet Rack, also known as Rivet Pallet Rack.
Frames of Pallet Rack
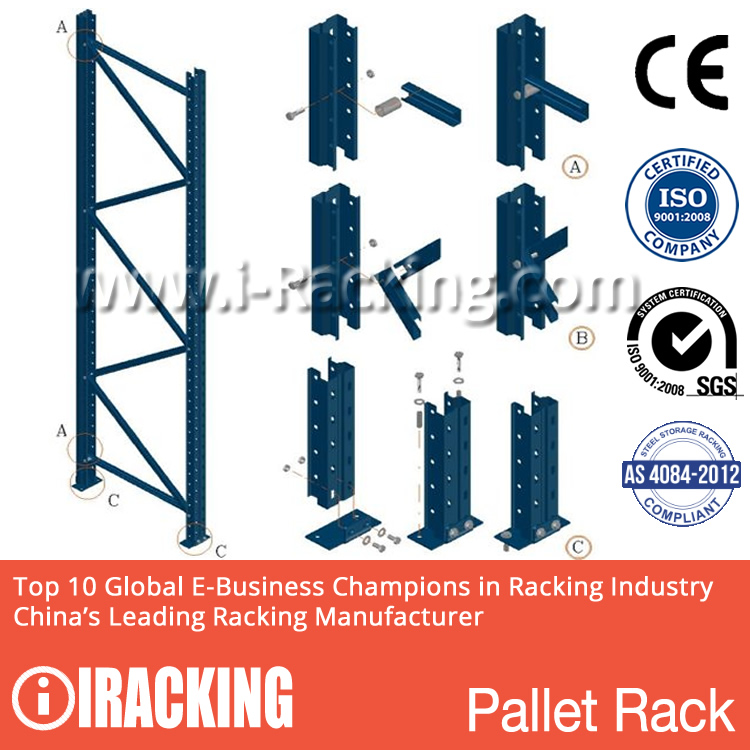
Each end frame is made up of two uprights with the corresponding horizontal and diagonal bracings, footplates, bolts & nuts and anchor bolts.
The depth of frame is determined by the size of the pallet. For a Europallet measuring 1,200mm deep, a 1,100 deep frame is normally used.
Uprights of Pallet Rack
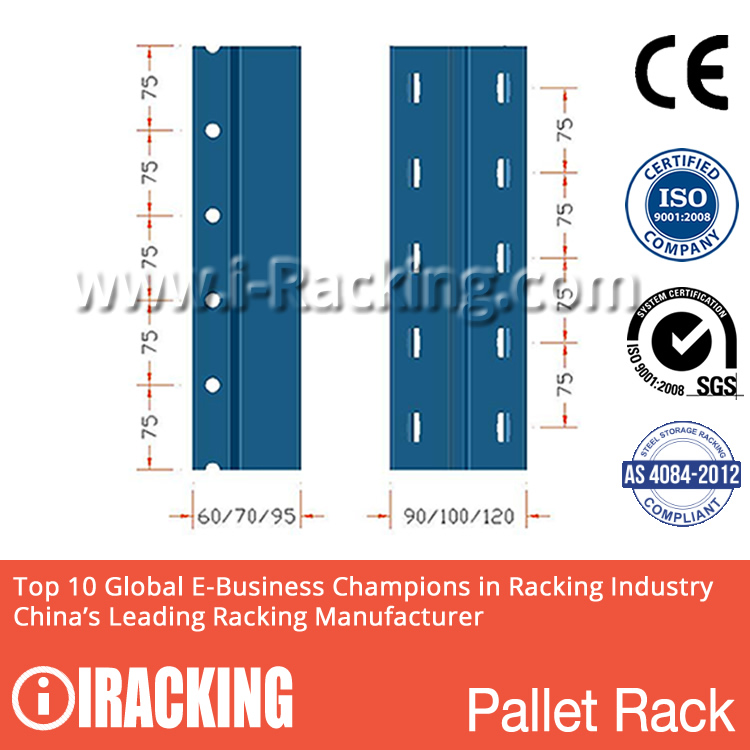
The different models, sections and thicknesses of uprights enable them to be adapted to a wide range of loading requirements. Uprights are punched with symmetric hexagonal slots at 75mm or 76.2mm intervals for beam height adjustment and are reversible.
Horizontal & Diagonal Bracings of Pallet Rack
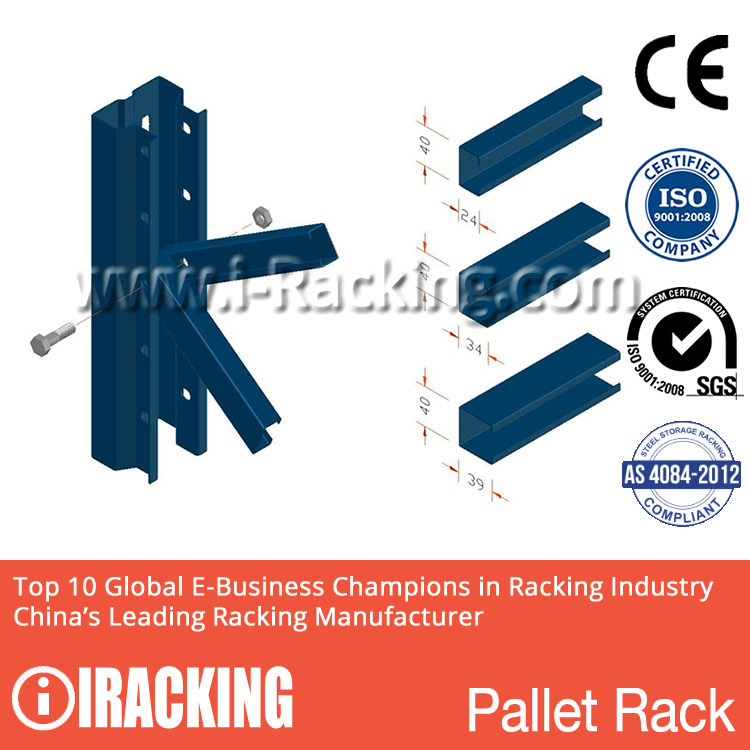
Frame Footplates of Pallet Rack
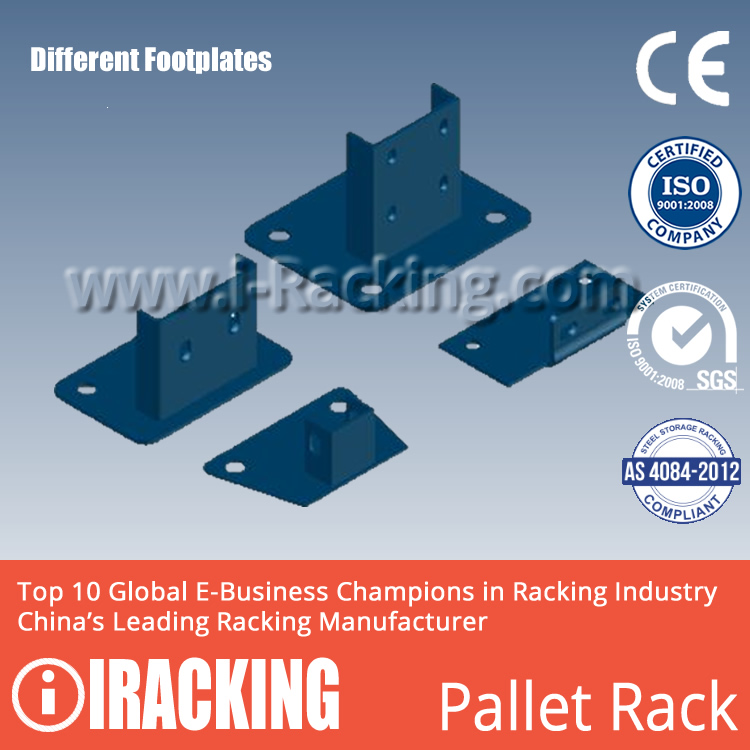
Frames are stood on the floor using footplates which are fitted to the base of the uprights. There is a range of different frame footplates whose use depends onthe load to be supported and on the upright model used. They are anchored to the floor using one or two anchor bolts.
Anchor Bolts and Safety Pins
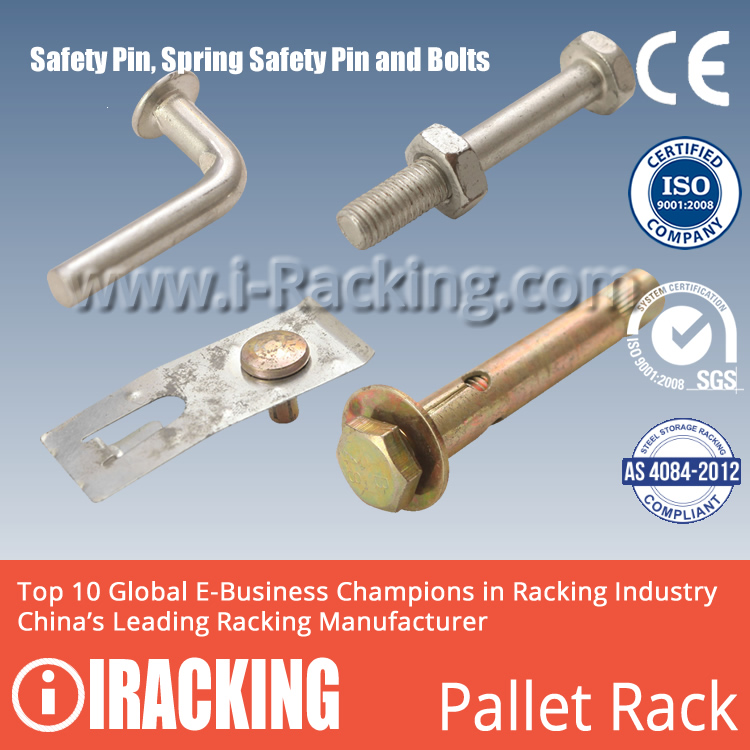
Racks are fixed to the slab using anchor bolts. They vary depending on the forces they have to withstand and the characteristics of the slab itself.
Two safety pins (Optional: Spring Safety Pins) are located into each beam to give additional protection against the beam dislodging whilst in use.
Frame Crash Barriers and Upright Protectors
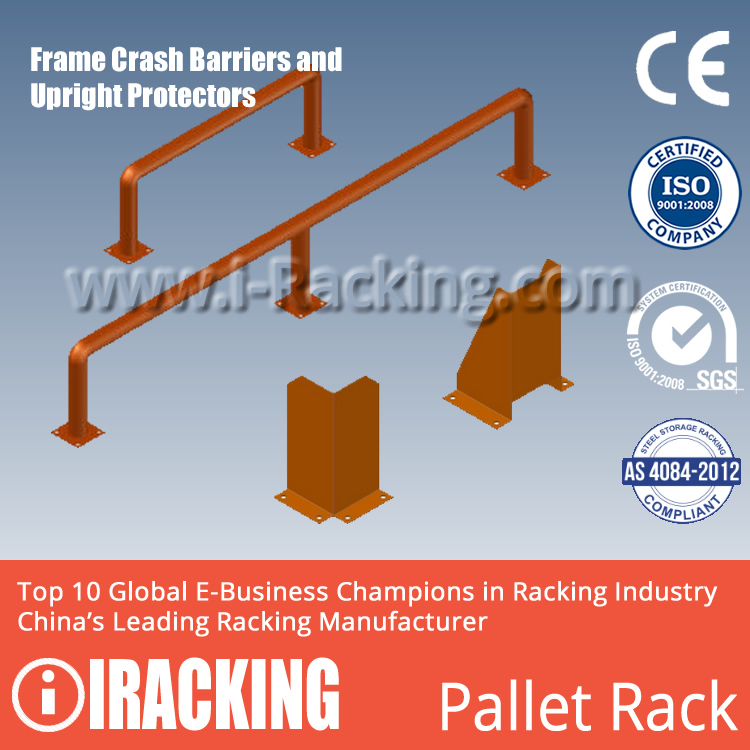
These protect the side of the rack base. It is normally fitted to end frames and in passageways between frames where impacts are more vulnerable.
These protect racks from light impacts that may occur at floor level, preventing the vertical components from local damage.
Box Beams of Pallet Rack
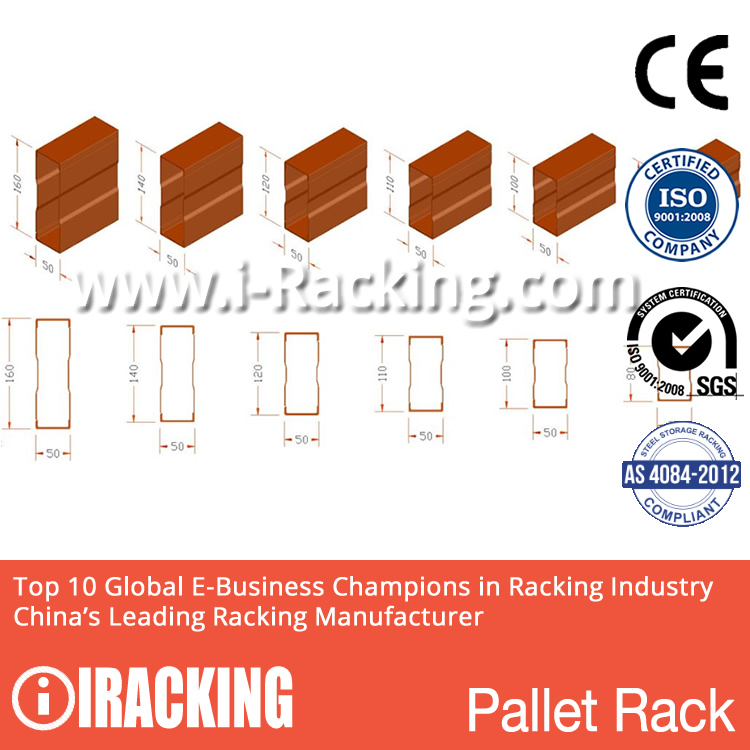
IRACKING provides a wide range of box beam section sizes to suit different needs of loading capacities.
Connectors
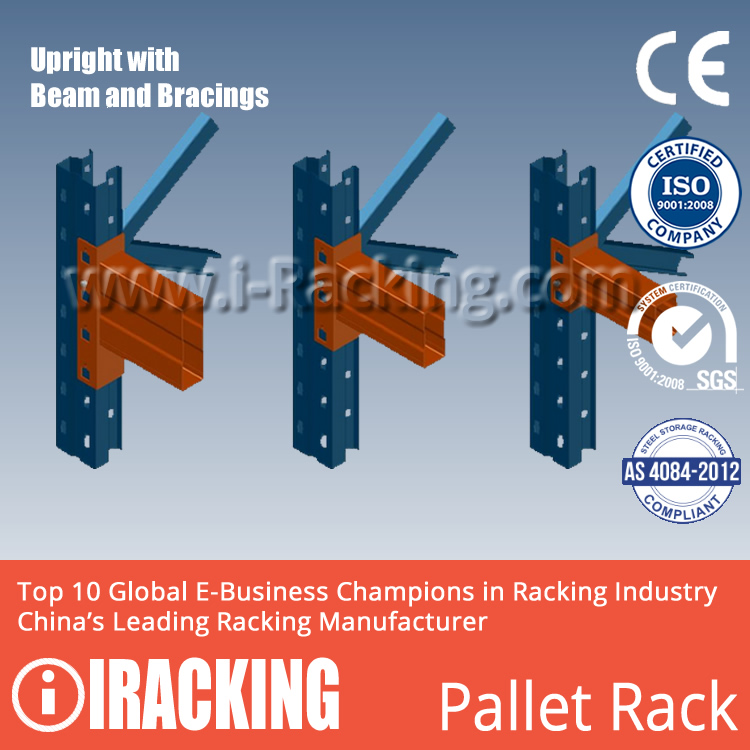
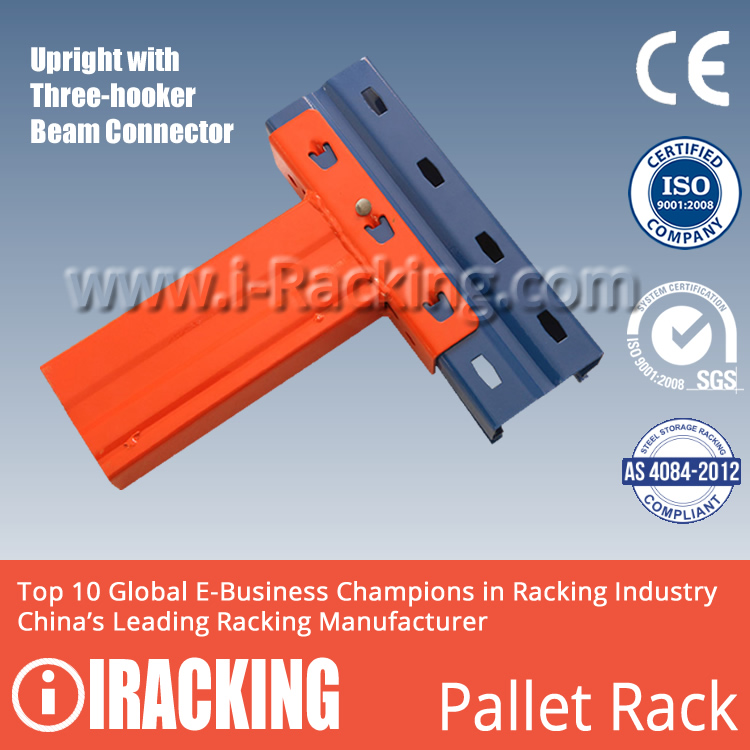
Mesh Deck for Pallet Rack (Optional)

Mesh Deck Show
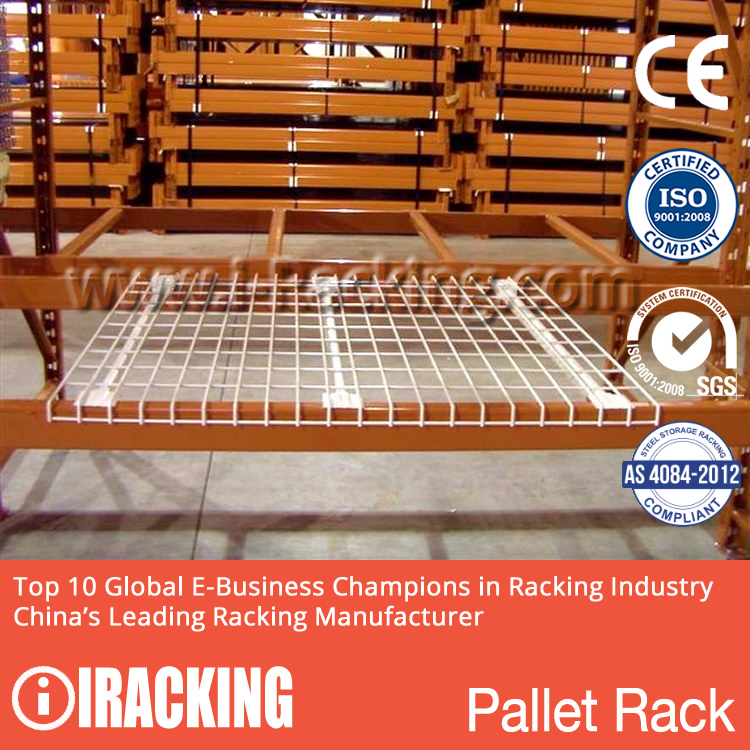
Mesh Deck for Pallet Rack (Optional)
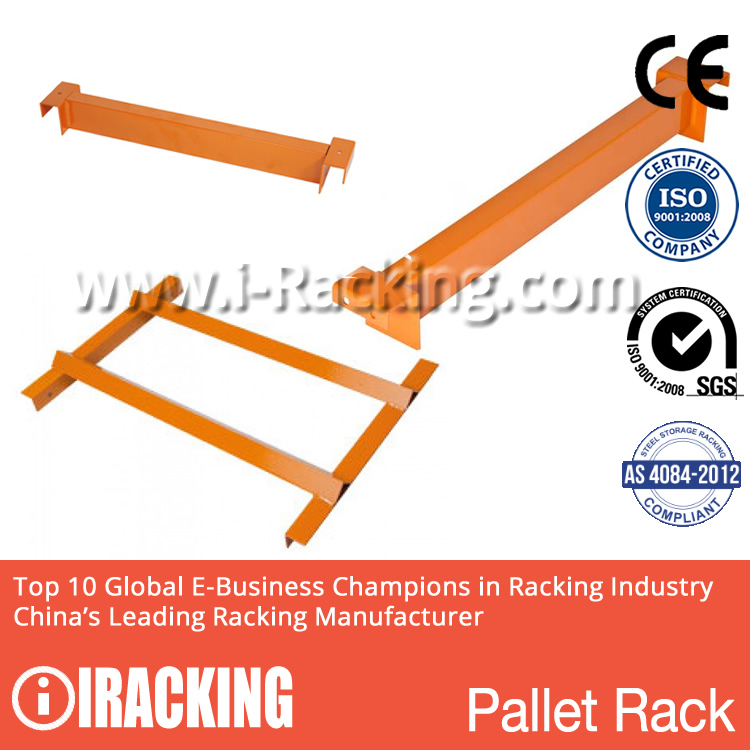
IRACKING provides different support bars to suit different storage needs, including Coil Support Bars.
Finishes
Option 1: Complete set with powder coating finish. Other colours are also available.
Powder epoxy-polyester coating, polymerized at 180℃, lead free.
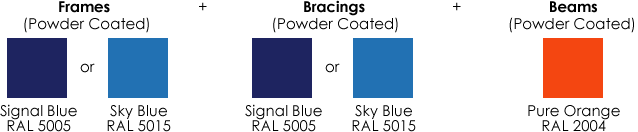
Option 2: Frames (including Uprights and Horizontal & Diagonal Bracings) pre-galvanized, Beams with powder coating finish.
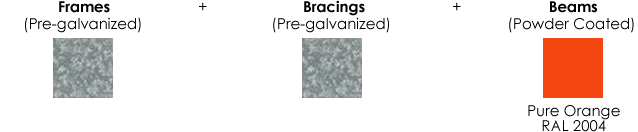
Option 3: Uprights & Beams with powder coating finish, Horizontal & Diagonal Bracings pre-galvanized.
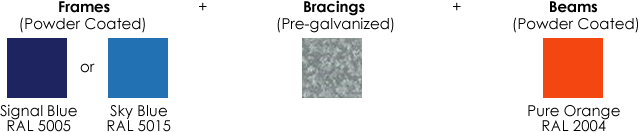
Production Management and Services
1. Quality Management Process is standardized, quantified, and traceable.
2. Raw materials suppliers are selected prudently. Selected Q235 rolled steel strips are tested and the physical properties must meet our internal standards.
3. The raw material thickness must fall within the specified tolerance.
4. The samples of each batch of raw materials are kept for 5 years for quality traceability.
5. Each batch of raw material is tested for tensile strength, yield strength, and elongation at break. Test reports are kept in our QA system and traceable. Batch sampling rate has rosen from 50% to 100%.
6. Only experienced workers and operators are employed, followed by our internal professional training.
7. Each process of production is guided and instructed by our technical department.
8. QA is incorporated into each and every production process. Only qualified products will flow into the next process.
9. The maximum load of each type of our standardized products is tested, complemented with random sample load test for finished products.
10. Load test for non-standardized products is carried out for each batch.
We provide standard packaging and small bundle retail packaging, as requested.
The design is an essential part of the process.
iRacking provides you a complete design matching your needs free of charge.