DRIVE IN RACK
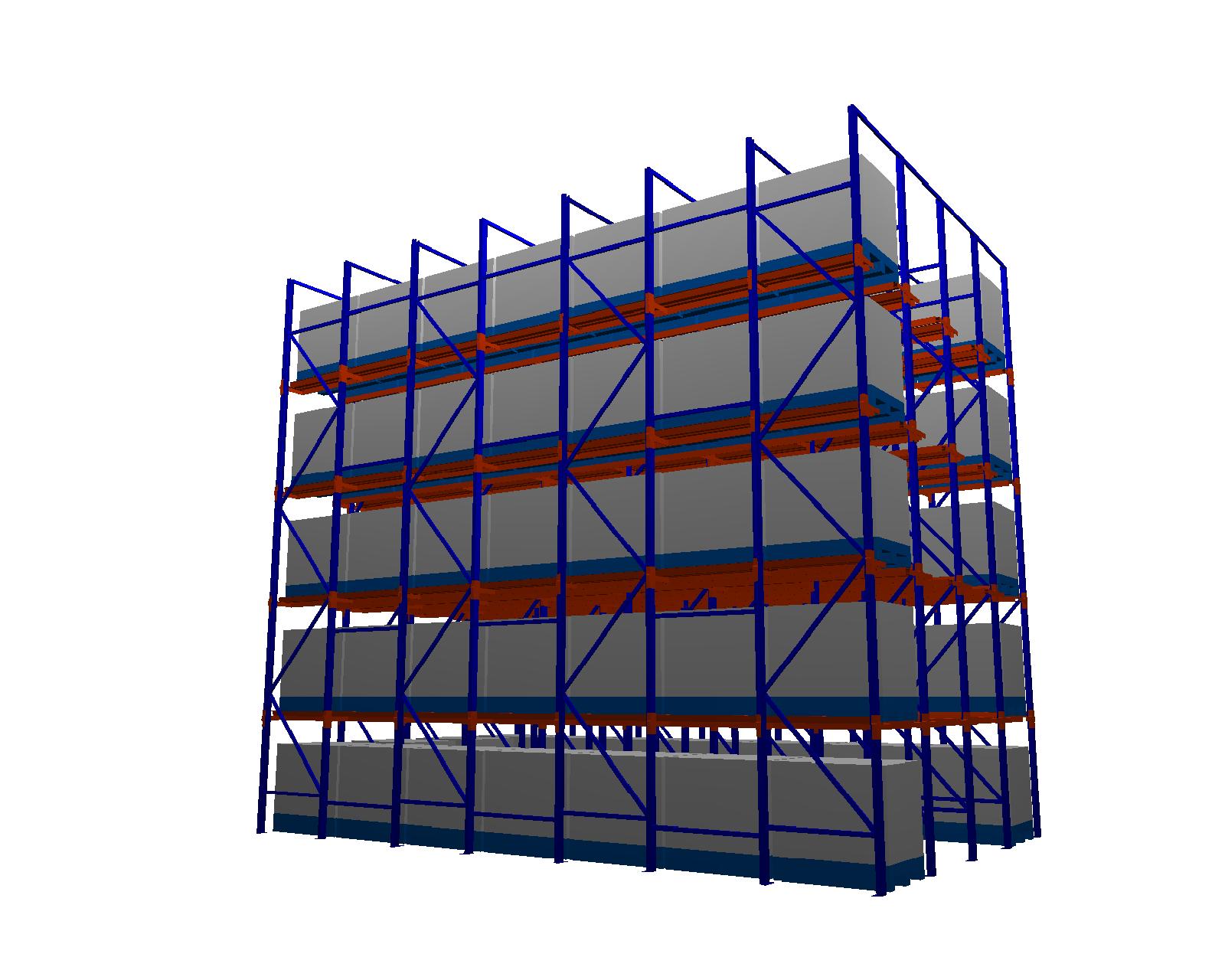
iRacking drive-in rack is designed for the storage of homogenous products. It accommodates a large number of pallets for each SKU.
The most high density system provides the maximum space efficiency and high volume storage of block stacking, with easy access to pallets.
This type of installation is made up of a set of racking units that form innter loading aisles, with support rails for the pallets. The forklift trucks enter these inner aisles with their load held higher than the level at which it is to be deposited.
Each loading asile has support rails on both sides. These are arranged on different levels and the pallets are placed on top. This racking system is made of extremely robust material, thus making it suitable for storing fully-loaded pallets.
Related Products
For different warehouse layouts, we also provide similar products, including Conventional Pallet Rack, Double Deep Pallet Rack, and Very Narrow Aisle (VNA) Rack. For US market, we supply US style Teardrop Pallet Rack, also known as Rivet Pallet Rack.
Features:
1 Good solution for storage of homogenous products with a great number of pallets.
2 Very highly efficient use of warehouse space.
3 Loading capacity 500kgs-1500kg/pallet as general.
4 Load management: FILO (First In, Last Out) or FIFO (First In, First Out).
5 Rails adjustable optimize space utilization.
6 Easy assembly.
Why IRACKING Drive In Rack?
1 Only high-quality RAW STEEL, by largest steel factories in China, is used for our racking products.
2 With large scale production, we are in a good position to lower product costs without compromising quality.
3 A wide range of different racking types are offered to suit different storage needs.
4 We provide free but expert advice & proposed racking solutions for your kind reference.
5 Quick delivery. Within 25 days for ordinary order quantity.
Layout Design (Free of charge!)
The drive-in system can accommodate as many SKU’s as there are loading aisles. The number of pallets will depend on the depth and height of the loading aisles. It is advisable to store products with the same SKU in each loading aisl, in order to avoid unnecessary pallets manoeuvres. The depth of each aisle will depend on the number of pallets per SKU, the space available and the length of time they will be stored.
As shown in the following illustrations, the drive-in system has a greater storage capacity than the conventional pallet racking system.
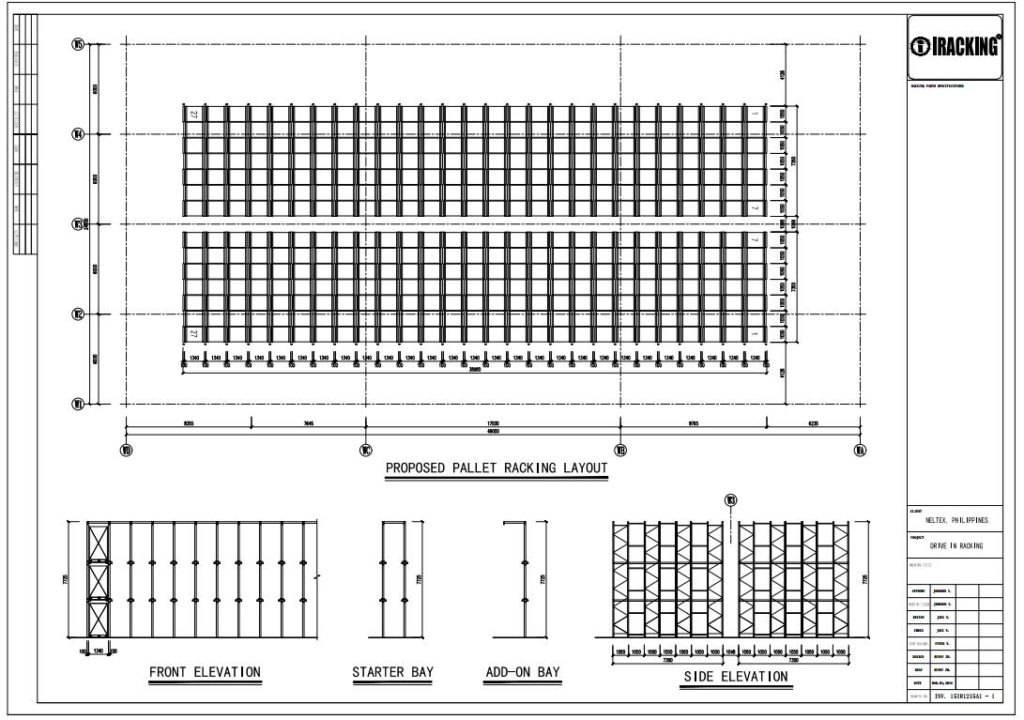
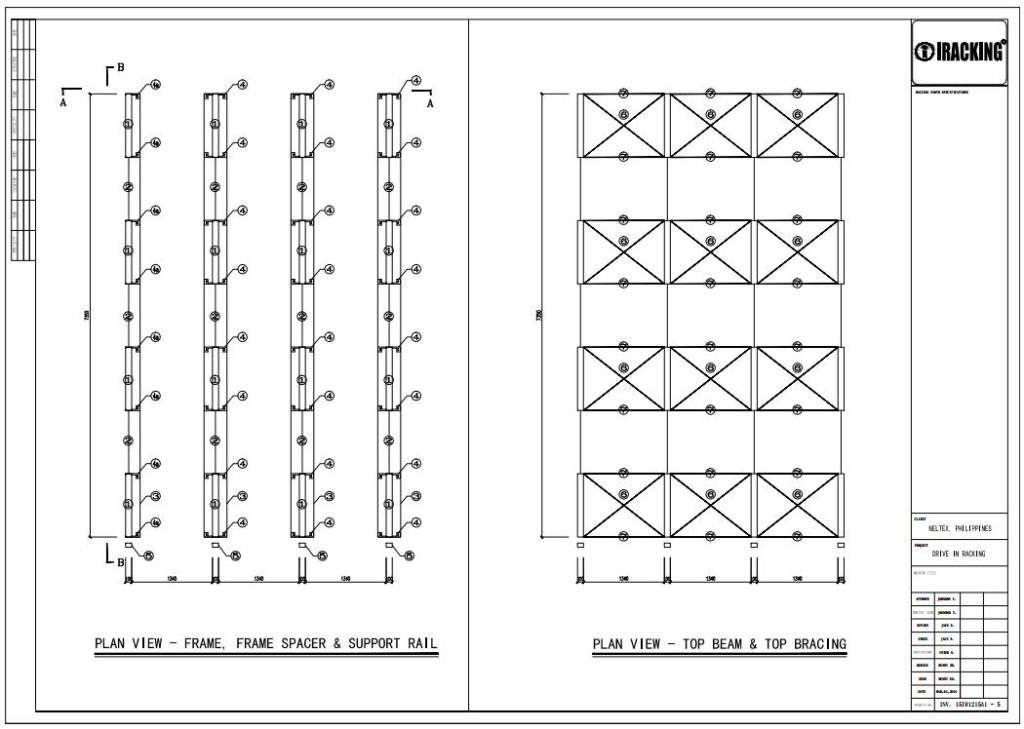
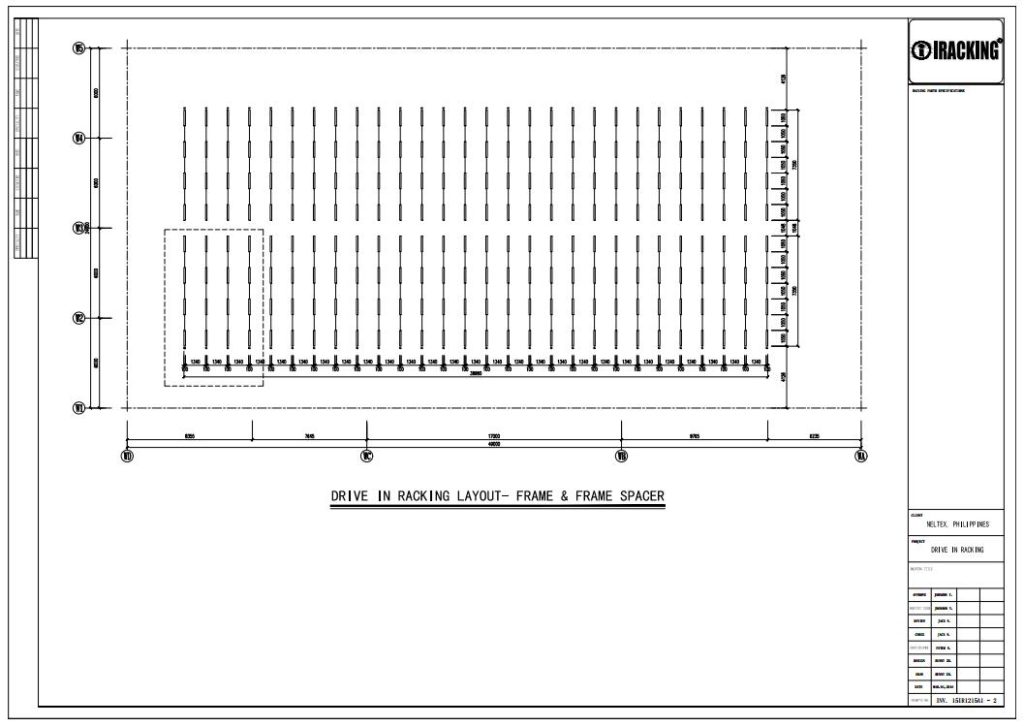

Frames
Frames are made up of two uprights with the corresponding horizontal& diagonal bracings, footplates and accessories.
The frames have slots every 75mm to accommodate the beams and supports.
The depth of the frame is determined by the dimensions of the storage aisle and the pallet height, measurements and weight.
IRACKING provides a wide range of post section sizes and thickness to suit different loading requirements.
Arms
There are two types of arms, which are single arm (left side and right side single arms) and double arm. The single arm is used in each side of the racks, while the double arm is used in between.
1 High-strength steel is used to make IRACKING drive-in racking arms.
2 Raw steel for beam connectors is tested by independent 3rd party of authoritative test organization.
3 Three-hooker with great loading capacity.
4 Beam load is correctly dissipated vertically down the front face of the upright.
5 Safety pin is located into each beam connector to give additional protection against the beam disloging whilst in use.
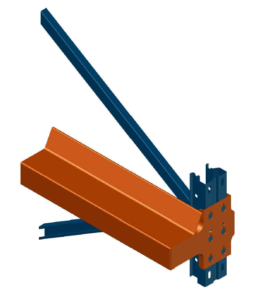
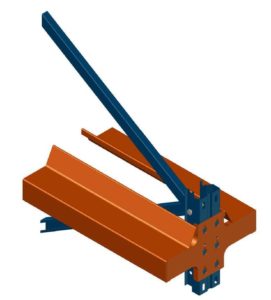
Pallet Support Rails
Support rails are stamp formed and the length can be customized. The rails are designed without connectors to ensure uniform loading.
1 High-strength steel is used to make IRACKING drive-in racking arms.
2 Uniform heavy duty loading
3 Support rail profiles enable pallet loads to be centralised and placed perfectly everytime.
Top beams and top bracings
Top beams and top bracings are used to increase integrity and stability of the racking system.
Production Management and Services
Quality Management and Control
1. Quality Management Process is standardized, quantified, and traceable.
2. Raw materials suppliers are selected prudently. Selected Q235 rolled steel strips are tested and the physical properties must meet our internal standards.
3. The raw material thickness must fall within the specified tolerance.
4. The samples of each batch of raw materials are kept for 5 years for quality traceability.
5. Each batch of raw material is tested for tensile strength, yield strength, and elongation at break. Test reports are kept in our QA system and traceable. Batch sampling rate has rosen from 50% to 100%.
6. Only experienced workers and operators are employed, followed by our internal professional training.
7. Each process of production is guided and instructed by our technical department.
8. QA is incorporated into each and every production process. Only qualified products will flow into the next process.
9. The maximum load of each type of our standardized products is tested, complemented with random sample load test for finished products.
10. Load test for non-standardized products is carried out for each batch.
We provide standard packaging and small bundle retail packaging, as requested.
The design is an essential part of the process.
iRacking provides you a complete design matching your needs free of charge.